Organisation lean et ergonomie d'une répartition pharmaceutique
Le magasin "déballé" réalise du picking pour composer les colis commandés par les pharmaciens.
Il est approvisionné par le magasin caisse (stockage de palettes sur racks).
Les colis constitués sont cerclés et transférés dans la zone expédition.
Le magasin M09 correspond à une zone de picking de produits conservés à 4°C.
Le magasin M10 correspond au magasin sous-clé.
Le périmètre de l’étude correspond aux magasins 01 à 07.
Les 7 magasins de l'étude sont composés de 330 racks de 6 étages de 140cm de long, avec pour chaque étage, des emplacements pour 4 références. Soit 24 références par rack (capacité maximale de 7920 références).
Présentation du projet de transformation du magasin de répartition pharmaceutique
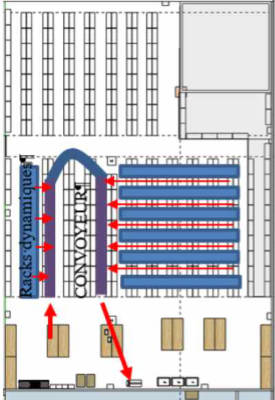
Le projet consiste à optimiser le processus de collecte en déplaçant un bac de poste en poste sur un convoyeur.
Un rack dynamique le long du convoyeur est envisagé pour les références à très fort volume ; il s’agirait pour les racks dynamiques de placer directement les cartons.
Pour les références à fort et moyen volume, les racks actuels seraient positionnés perpendiculairement au convoyeur. Pour les petits volumes, le mode collecte serait le même qu’aujourd’hui.
Ci-contre, le principe général d’implantation souhaité avec un flux (flèche rouge) consistant à envoyer des bacs sur le convoyeur et les expédier à la sortie du convoyeur.
Simulations pour optimiser l'implantation
Une analyse des données montre que 920 références (environ 20% du nombre de références)représentent environ 80% du volume de produits diffusés Cette donnée est un repère pour tester différentes possibilités. La longueur initialement envisagée du rack dynamique a été augmentée afin de pouvoir absorber plus de références.
Deux hypothèses d'implantation
Hypothèse 1 (à gauche) : Les 920 références ne peuvent pas être absorbées uniquement par les racks dynamiques malgré l'augmentation de la longueure.
La prise en compte des premiers racks (en rouge) sur le retour du convoyeur permet d’absorber les 1060 références à plus fort volume.
Hypothèse 2 (à droite) consiste à réduire le nombre de racks dynamique pour permettre l’accès au convoyeur à un opérateur chargé de la régulation des flux.
Pour compenser la réduction du nombre de références en rack dynamique (de 640 à 448 références) les deux premiers racks sur le retour du convoyeur sont affectés au plus gros volume (racks en rouge).
1288 références peuvent ainsi être positionnées au plus près du convoyeur.
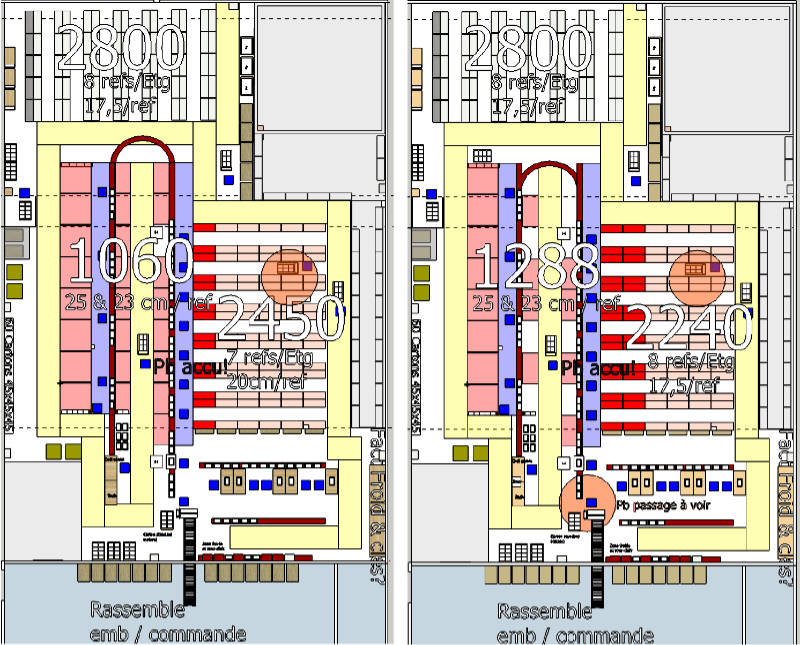
Présentation du projet d'implantation retenu
Les principales modifications retenues:
1-Les racks dynamiques sont moins logeant que prévu (-15% de références sur racks dynamiques) ; ceci est compensé par un passage de 6 à 8 références par étage pour les racks du MAG 1 proche du convoyeur (en rouge) ; ceci implique 1496 références.
2-compte tenu du nombre de 8 références par étage, il convient de prévoir des bacs tiroirs pour dé-coliser en dehors des allées. Cela implique de créer des postes à cet effet ce qui conduit à une réduction du nombre de racks
(voir à droite du plan le long de l'allée et ci-dessous la première image).
3-L’allée principale de circulation (en jaune) est de 1800mm de large afin de permettre de se croiser en déplaçant des palettes. (Réduction du nombre de racks).
4-le passage entre racks est augmenté de 900 à 1000 pour faciliter les mouvements de réapprovisionnement.
Tous ces points expliquent le passage d'une capacité de 6328 références à 5816 références (pour un besoin actuel de 4600).
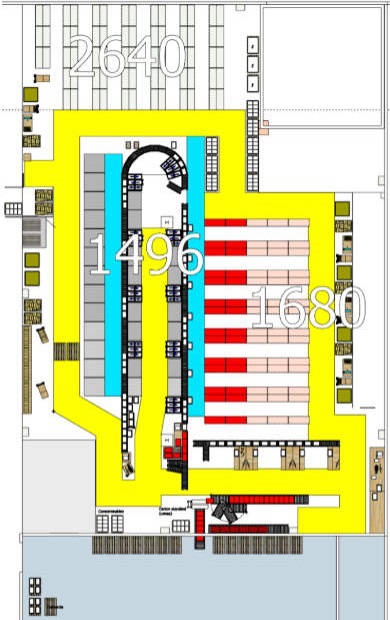
Quelques vues de détail
Vue de la zone prévue pour déballer les caisses pour approvisionner les racks de références à fort volume
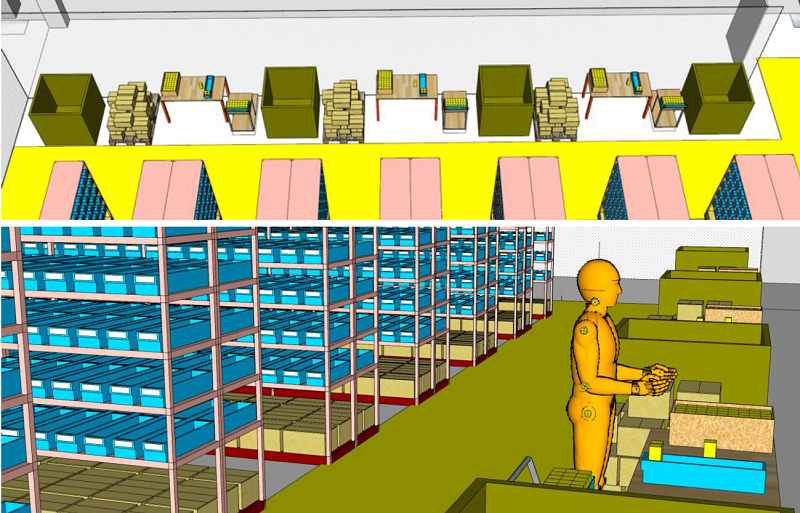
Vue en plan des racks dynamiques et du convoyeur
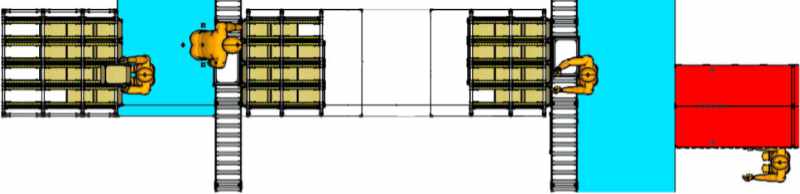
Zone de déballage des caisses pour approvisionner les racks de références à faible volume
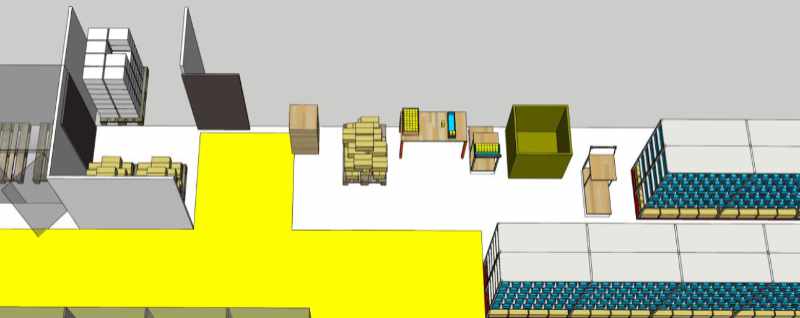
Détail des racks dynamique prévus
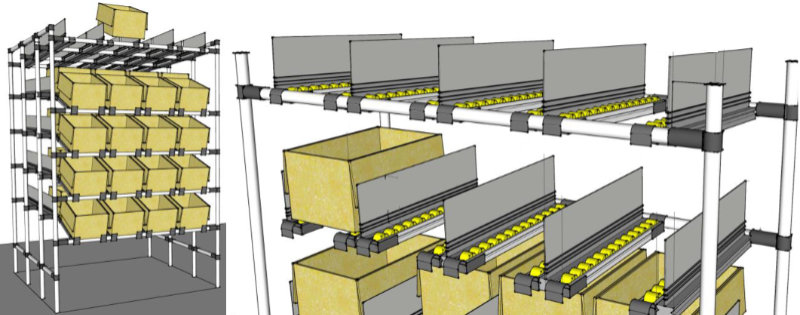
Présentation des principaux postes
Le poste de lancement sur convoyeur
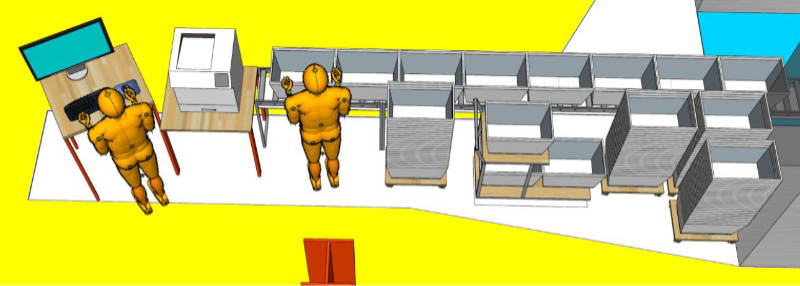
Le poste de réception du picking
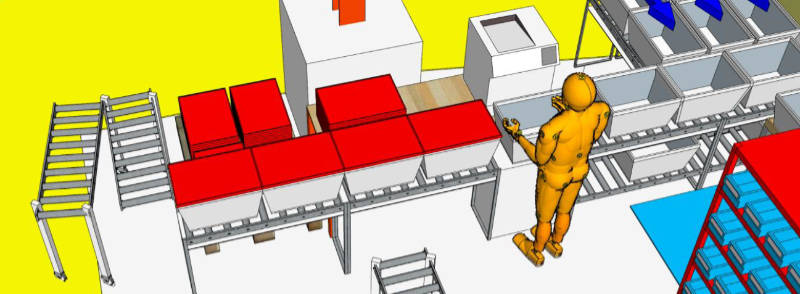
Le poste de contrôle (à noter le plan à deux niveaux pour optimiser la sortie des produits du bacs et leur rangement après vérification
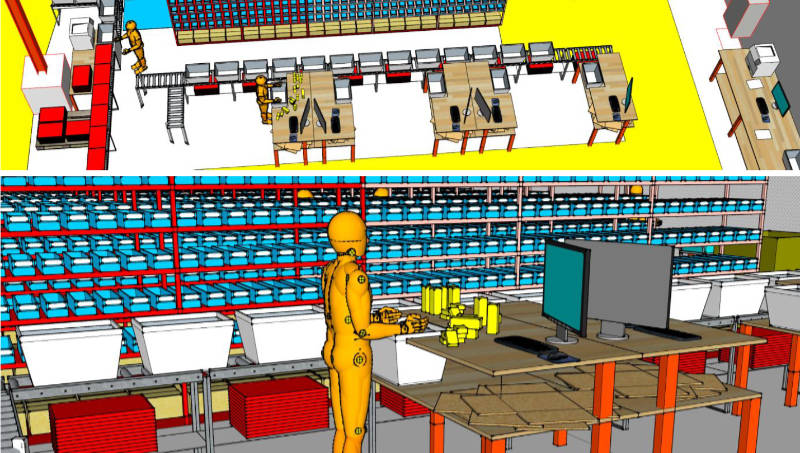
Le poste d'expédition de la commande client
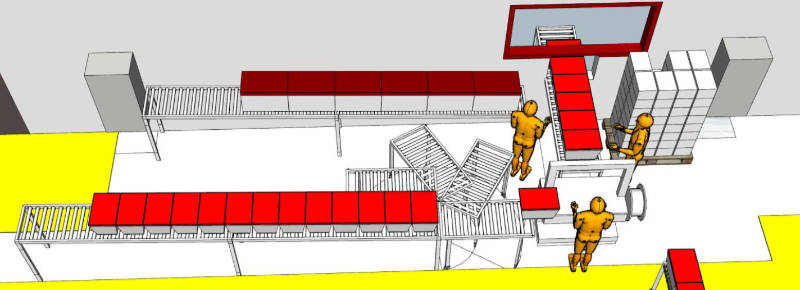